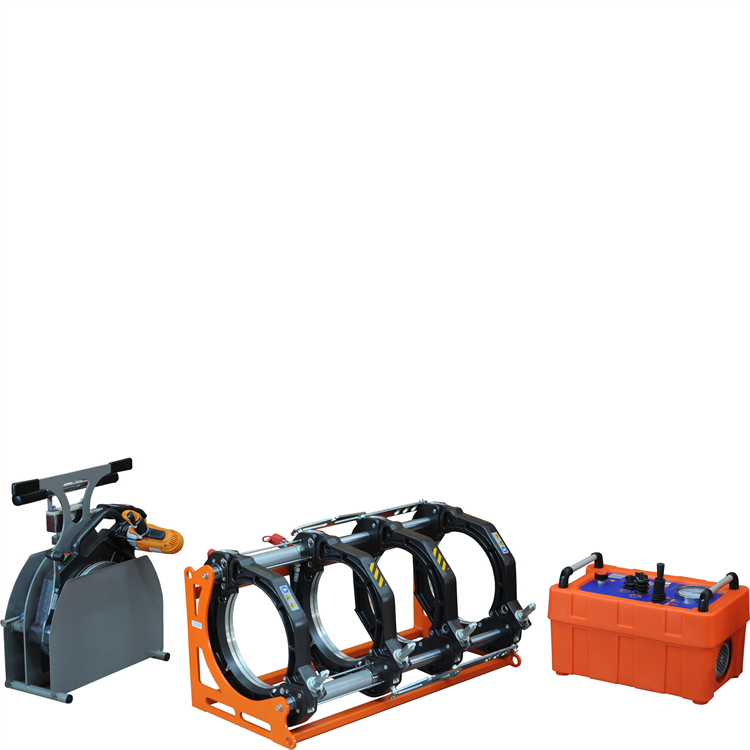
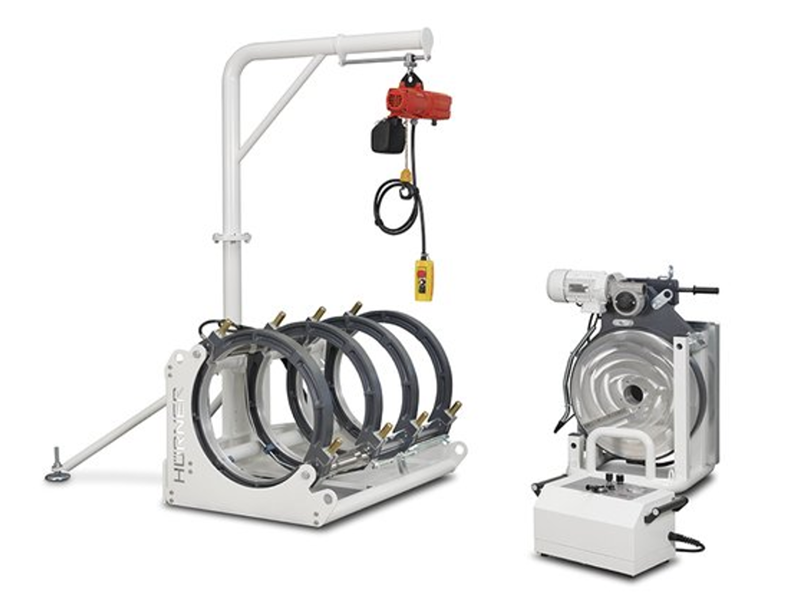
Hva er en Speilsveis Maskin og Hvorfor er Den Essensiell?
En speilsveis maskin, også kjent som en termoplastisk sveiseenhet, er et spesialdesignet verktøy som brukes til å skjøte termoplastiske rør og fittings ved hjelp av varme. Denne metoden, kalt speilsveising, gir sterke og pålitelige skjøter som er avgjørende for en rekke applikasjoner, fra VVS-installasjoner i boliger til komplekse industrielle rørsystemer. I motsetning til andre sveisemetoder, involverer speilsveising samtidig oppvarming av endeflatene på de to komponentene som skal skjøtes, før de presses sammen under kontrollert trykk for å danne en permanent, homogen forbindelse. Dette resulterer i en skjøt som ofte er like sterk som selve rørmaterialet.
Behovet for en pålitelig speilsveis maskin er kritisk i bransjer som rørlegging, kjemisk industri, landbruk (for irrigasjonssystemer) og i konstruksjon av svømmebasseng. Kvaliteten på sveiseskjøtene har direkte innvirkning på levetiden og sikkerheten til de installerte rørsystemene. En dårlig utført sveising kan føre til lekkasjer, kostbare reparasjoner og i verste fall farlige situasjoner.
De Forskjellige Typene Speilsveis Maskiner Du Bør Kjenne Til
Markedet tilbyr et bredt spekter av speilsveis maskiner, designet for ulike behov og bruksområder. Å forstå de forskjellige typene vil hjelpe deg med å velge den maskinen som best passer dine spesifikke krav.
Manuelle Speilsveis Maskiner: Enkelhet og Portabilitet
Manuelle speilsveis maskiner er ideelle for mindre prosjekter og reparasjoner, samt for bruk på trange steder hvor mobilitet er viktig. Disse maskinene krever manuell betjening for å påføre trykk og kontrollere sveisesyklusen. De er ofte lettere og mer kostnadseffektive enn de mer avanserte modellene, noe som gjør dem populære blant gjør-det-selv entusiaster og mindre bedrifter.
Hydrauliske Speilsveis Maskiner: Kraft og Presisjon
Hydrauliske speilsveis maskiner er designet for større og mer krevende prosjekter som involverer større rørdimensjoner. De bruker et hydraulisk system for å generere og opprettholde det nødvendige trykket under sveisingen, noe som sikrer jevne og pålitelige skjøter. Disse maskinene tilbyr høyere presisjon og kontroll over sveiseprosessen, noe som er avgjørende for kritisk infrastruktur og industrielle applikasjoner.
CNC Speilsveis Maskiner: Automatisering og Effektivitet
CNC (Computer Numerical Control) speilsveis maskiner representerer det ypperste innen sveiseteknologi for termoplastiske rør. Disse maskinene automatiserer hele sveiseprosessen, fra oppvarming til sammenføyning og kjøling, basert på forhåndsprogrammerte parametere. Dette minimerer risikoen for menneskelig feil, øker produktiviteten og sikrer konsistent høy kvalitet på alle sveiseskjøter. CNC-maskiner er ideelle for storskala prosjekter og produksjonslinjer hvor effektivitet og repeterbarhet er avgjørende.
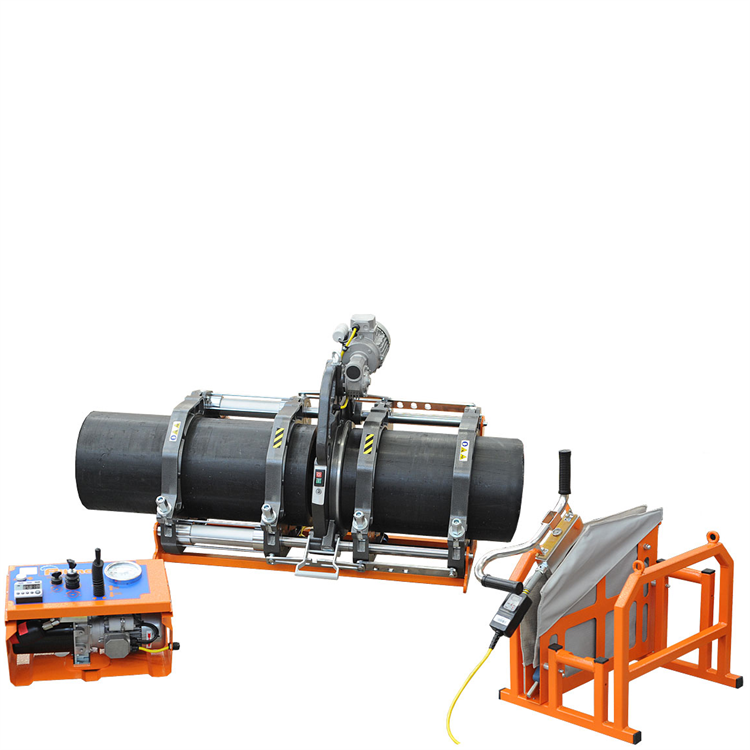
Elektromuffe Sveiseapparater: Et Alternativ til Speilsveising
Selv om det ikke er en speilsveis maskin i tradisjonell forstand, er elektromuffesveising en annen vanlig metode for å skjøte plastrør. Elektromuffesveiseapparater bruker elektrisk motstand innebygd i en muffe for å smelte sammen muffen og rørenden. Denne metoden er spesielt nyttig for sammenføyning av rør i grøfter eller på vanskelig tilgjengelige steder, da den krever mindre plass rundt røret.
Hvordan en Speilsveis Maskin Fungerer: Steg-for-Steg
For å oppnå en perfekt speilsveising er det viktig å forstå de grunnleggende trinnene i prosessen:
- Forberedelse av Rørene: Endene på rørene som skal skjøtes må kuttes rent og vinkelrett. Eventuell smuss, fett eller oksidasjon må fjernes grundig for å sikre en optimal smelteprosess.
- Oppvarming: En oppvarmingsplate, belagt med et non-stick materiale og oppvarmet til en spesifikk temperatur (avhengig av rørmaterialet), presses mot de forberedte rørendene. Varmen smelter overflatene av rørene jevnt.
- Fjerning av Varmeplaten: Når rørendene har nådd riktig smeltegrad og -dybde, fjernes varmeplaten raskt og forsiktig for å unngå forstyrrelser.
- Sammenføyning: De smeltede rørendene føres raskt sammen og presses mot hverandre med et forhåndsbestemt trykk. Det er viktig at denne prosessen skjer raskt for å sikre en god fusjon av materialene.
- Kjøling: Den sammensveisede skjøten holdes under konstant trykk i en bestemt kjøleperiode. Dette gjør at smelte kan stivne ordentlig og danne en sterk, homogen forbindelse.
Nøyaktig kontroll av temperatur, trykk og tid er avgjørende for en vellykket speilsveising. Moderne speilsveis maskiner er ofte utstyrt med presise kontrollsystemer for å sikre optimale resultater.
Viktige Faktorer å Vurdere Når Du Velger en Speilsveis Maskin
Valget av riktig speilsveis maskin avhenger av en rekke faktorer. Her er noen av de viktigste aspektene du bør vurdere:
- Rørmateriale: Ulike termoplastiske materialer (som PP-R, PE, PB) krever forskjellige sveisetemperaturer og trykk. Sørg for at maskinen du velger er kompatibel med materialene du skal sveise.
- Rørdimensjoner: Speilsveis maskiner har vanligvis et spesifikt område av rørdimensjoner de kan håndtere. Velg en maskin som dekker de dimensjonene du oftest vil jobbe med.
- Prosjektomfang og Frekvens: For sporadisk bruk eller mindre prosjekter kan en manuell maskin være tilstrekkelig. For større, mer intensive prosjekter vil en hydraulisk eller CNC-maskin sannsynligvis være en bedre investering.
- Portabilitet: Hvis du trenger å flytte maskinen ofte mellom forskjellige arbeidssteder, er en lett og kompakt modell med et robust design viktig.
- Budsjett: Prisen på speilsveis maskiner kan variere betydelig avhengig av type, kapasitet og funksjoner. Sett et realistisk budsjett og undersøk hvilke alternativer som er tilgjengelige innenfor dette.
- Funksjoner og Kontroller: Avanserte maskiner kan tilby funksjoner som digital temperaturkontroll, trykkregulering, datalogging og forhåndsprogrammerte sveiseparametere. Vurder hvilke funksjoner som er viktige for dine behov.
- Kvalitet og Pålitelighet: Investér i en maskin fra en anerkjent produsent med gode tilbakemeldinger for kvalitet og pålitelighet. Dette vil sikre lang levetid og redusere risikoen for driftsstans.
- Service og Support: Sjekk tilgjengeligheten av reservedeler, service og teknisk support fra leverandøren. God support kan være avgjørende hvis det oppstår problemer med maskinen.
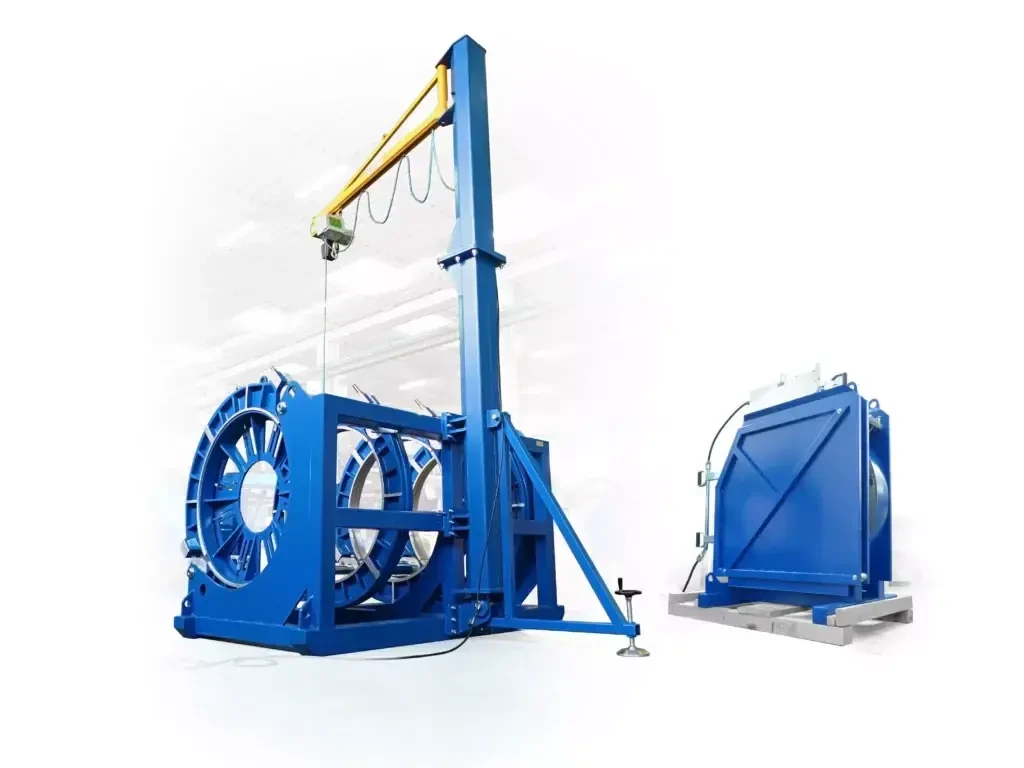

Tips for Perfekt Speilsveising med Din Maskin
Selv med den beste speilsveis maskinen er det viktig å følge riktig prosedyre for å oppnå perfekte sveiseskjøter:
- Rengjør grundig: Sørg alltid for at rørendene og varmeplaten er rene før sveising. Selv små partikler kan svekke skjøten.
- Bruk riktig temperatur: Følg produsentens anbefalinger for sveisetemperatur for det spesifikke rørmaterialet du arbeider med. Feil temperatur kan føre til dårlig fusjon.
- Påfør riktig trykk: Bruk det anbefalte trykket under oppvarming og sammenføyning. For lavt trykk kan gi en svak skjøt, mens for høyt trykk kan deformere rørene.
- Overhold sveisetidene: Følg de anbefalte oppvarmings- og kjøletidene nøye. For kort oppvarming kan føre til dårlig fusjon, mens for lang oppvarming kan skade materialet.
- Unngå forstyrrelser under kjøling: Ikke beveg eller belaste skjøten før den har kjølt seg ned tilstrekkelig.
- Utfør visuell inspeksjon: Etter sveisingen, inspiser skjøten nøye for eventuelle defekter som ujevnheter, sprekker eller manglende fusjon.
- Vedlikehold maskinen din: Regelmessig rengjøring og vedlikehold av speilsveis maskinen vil sikre optimal ytelse og forlenge levetiden.
Konklusjon: Invester i Kvalitet for Pålitelige Resultater
En pålitelig speilsveis maskin er en uvurderlig investering for alle som arbeider med termoplastiske rørsystemer. Ved å forstå de forskjellige typene maskiner, vurdere dine spesifikke behov og følge riktig sveiseprosedyre, kan du sikre sterke, holdbare og lekkasjefrie skjøter. Enten du er en erfaren profesjonell eller en engasjert gjør-det-selv entusiast, vil valget av riktig speilsveis maskin og nøye utførelse av sveisearbeidet være nøkkelen til suksess.
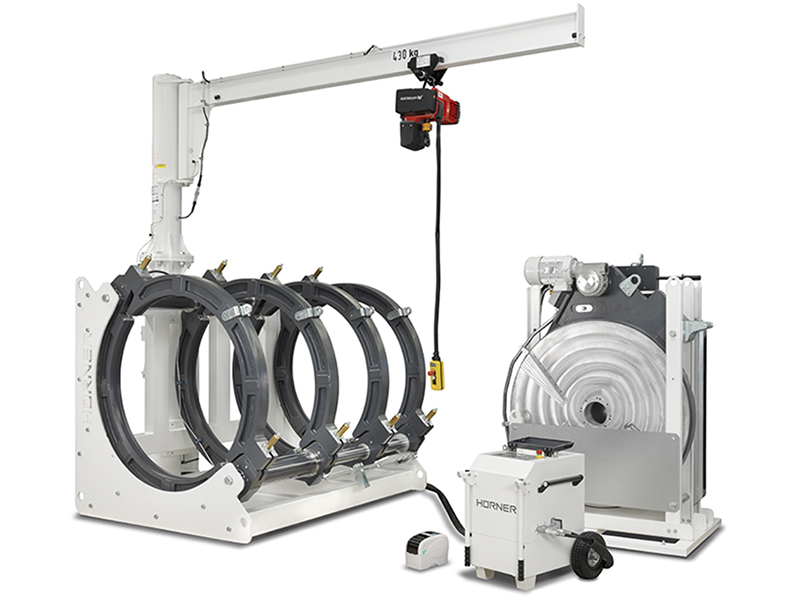
Utforsk vårt utvalg av høykvalitets speilsveis maskiner og finn den perfekte løsningen for dine prosjekter. Kontakt oss i dag for ekspertråd og veiledning!